5S by Hiroyuki Hirano
Hiroyuki Hirano’s 5S is a system for organizing the workplace. It consists of five steps: Sort, Set in order, Shine, Standardize, and Sustain. The goal of 5S is to create a safe and efficient workspace.
The first step in 5S is Sort. This means that all unnecessary items should be removed from the workspace. This will help to reduce clutter and make it easier to find what you need.
The second step is Set in order. This means that everything should have a place and be organized in a way that makes sense. This will help you to know where everything is and make it easy to find what you need.
The third step is Shine. This means that the workspace should be cleaned on a regular basis. A clean workspace will help to prevent accidents and improve efficiency.
The fourth step is Standardize. This means that there should be standard procedures for how tasks are completed in the workspace. Having standard procedures will help to ensure that tasks are completed safely and efficiently.
The fifth and final step is Sustain. This means that the 5S system must be maintained over time in order to continue reaping its benefits.
In the business world, efficiency is key to success. That’s why many organizations implement 5S programs, which are designed to improve workplace productivity and quality. Hiroyuki Hirano’s 5S is a popular method for achieving these goals.
The 5S system includes five steps: sort, set in order, shine, standardize, and sustain. These steps can be implemented in any workplace to improve organization and cleanliness. In addition, 5S programs can help reduce waste and increase safety.
While some organizations may be hesitant to implement a 5S program because of the upfront cost or time commitment, the long-term benefits are clear. A well-run 5S program can lead to a more efficient workplace that is safer and easier to work in.
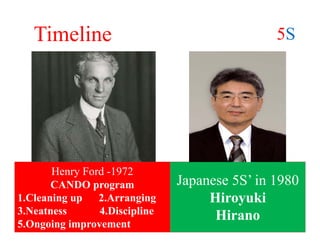
Credit: www.slideshare.net
What is the 5S System
The 5S system is a process improvement method that originated in Japan. The system is designed to help businesses keep their work areas organized, clean and safe. The 5S acronym stands for the following five Japanese words:
Seiri – Sort
Seiton – Set in order
Seiso – Shine
Seiketsu – Standardize
Shitsuke – Sustain
When properly implemented, the 5S system can lead to a number of benefits for businesses, including increased productivity, improved quality, reduced waste and lower costs.
What are the Benefits of Using the 5S System
The 5S system is a lean manufacturing tool that can be used in any type of business to improve efficiency and quality. The five “S”s stand for Sort, Set in Order, Shine, Standardize, and Sustain. Implementing the 5S system can help to eliminate waste, maximize space utilization, and create a safer and more organized work environment.
One of the main benefits of using the 5S system is that it can help to reduce or eliminate waste in your workplace. This is because one of the key components of the 5S system is sorting through everything in your workspace and getting rid of anything that is not absolutely necessary. This includes things like excess inventory, unused tools or equipment, and anything else that takes up valuable space without serving a purpose.
By decluttering your workspace and getting rid of unnecessary items, you can free up space and make it easier to find what you need when you need it. This can save time and increase productivity.
Another benefit of using the 5S system is that it helps to create a safe working environment.
This is because part of the “set in order” step involves labeling everything so that employees know where things are supposed to go (and where they shouldn’t go). This reduces the chances of accidents happening due to confusion or disorganization. In addition, by having everything in its place, you are less likely to trip over something or knock something over.
A well-organized workspace is a safe workspace.
Finally, using the 5S system can help improve employee morale by creating a more efficient workplace. Employees who have to search for things or who constantly feel like they are swimming in clutter are often unhappy at work.
On the other hand, employees who have everything they need within reach and who understand where things belong tend to be more contented with their jobs.
How Can I Implement the 5S System in My Workplace
The 5S system is a systematic approach to workplace organization and can be used in any industry. The system consists of 5 steps: Sort, Set in Order, Shine, Standardize, and Sustain.
1. Sort- The first step is to sort through all of the items in your workplace and get rid of anything that is not needed.
This will declutter your work area and make it easier to find things when you need them.
2. Set in Order- Once you have sorted through everything, it’s time to set up an organizational system that works for you and your team. This may include labeling storage areas, creating a cleaning schedule, or establishing where supplies will be kept.
3. Shine- Now it’s time to give your workplace a good cleaning! Get rid of all the dust and dirt so that your workspace is clean and inviting.
4. Standardize- This step involves creating standard operating procedures (SOPs) for tasks that are performed regularly in your workplace.
Having SOPs ensures that everyone knows how to do their job correctly and efficiently.
5. Sustain- The final step is to sustain the improvements you have made by maintaining the standards you have set in place with regular audits.
What are Some Common Mistakes Made When Implementing the 5S System
There are a few common mistakes that can be made when implementing the 5S system:
1. Not Defining the Purpose of the 5S System: The first step in successfully implementing the 5S system is to define the purpose for doing so. Without a clear purpose, it will be difficult to get buy-in from employees and sustain momentum over time.
2. Not Assigning Responsibility: Once the purpose of the 5S system has been defined, it’s important to assign responsibility for its implementation and ongoing maintenance. This will ensure that there is someone accountable for ensuring that the system is being followed and that improvements are being made on an ongoing basis.
3. Not Training Employees: Another common mistake is not providing training to employees on how to implement and follow the 5S system.
This can lead to confusion and frustration, which can jeopardize the success of the entire initiative.
4. Not Sustaining Momentum: Implementing the 5S system requires a lot of effort upfront, but it’s important to maintain momentum over time in order to realize benefits long-term. This often means setting up regular audits or check-ins to ensure that standards are being met and improvements are still being made.
5. Not Measuring Results: Finally, one of the most common mistakes is not measuring results throughout the implementation process. This makes it difficult to track progress and identify areas where further improvement is needed.
How Can I Troubleshoot Problems With My 5S Implementation
When it comes to Lean and the 5S methodology, troubleshooting is a necessary evil. Without proper troubleshooting, it’s impossible to identify and correct errors in your process. The goal of 5S is to streamline your process and make it more efficient, so if you’re not Troubleshooting along the way, you’re likely missing out on potential improvements.
There are a few different ways to approach Troubleshooting with 5S. First, you need to identify where the problem is occurring. Is it in the Sort stage?
Maybe there’s too much clutter and it’s making it difficult to find things. Or maybe the problem is in the Set In Order stage? Maybe things are organized but not in a way that makes sense for your process.
Once you’ve identified where the problem is occurring, you can start to brainstorm potential solutions.
If the problem is in the Sort stage, one solution could be to create more specific sorting criteria. This will help ensure that only relevant items are kept in each area, which will make it easier to find what you need when you need it.
Another solution could be to implement color-coding or labeling systems so that items are easy to identify at a glance. If the problem is in the Set In Order stage, possible solutions include creating standard operating procedures (SOPs) for each task or implementing visual management tools such as Kanban boards.
Once you’ve identified potential solutions, it’s time to test them out and see if they work!
Try implementing one or two solutions and see how they impact your process. If they seem to help, great! Keep using them moving forward.
5S – El Origen
Conclusion
Hiroyuki Hirano’s 5S blog post details the five steps of the 5S process. The first step is sorting, which means separating out the items you need from the ones you don’t. The second step is setting in order, which means organizing your workspace so that everything has a place.
The third step is shining, or cleaning up your workspace. The fourth step is standardizing, which means making sure that everyone follows the same procedures. The fifth and final step is sustaining, or maintaining the cleanliness of your workspace over time.